長距離移動に欠かせない航空機や、私たちの生活を支える火力発電にはタービンエンジン*が使われています。近年は燃費向上やCO2排出削減に向けた軽量化、エンジン出力を効率よく発揮するための燃焼温度の高温化の技術開発が進んでいますが、一方でタービン部材として使用される耐熱合金が燃焼温度の高温化に耐え切れなくなることが予想されています。
東ソーはこの耐熱合金に代わる材料としてセラミックスマトリックスコンポジット(CMC)に着目しました。というのもCMCは、製品化している製品のジルコニア*と「傷に強いセラミックス」という共通項があり、知見やノウハウを生かせると思い、CMC開発に着手しました。
-
タービン(回転式の原動機)を回すことで動力を得るエンジン。
目次
CMCとは
CMCは、セラミックス繊維をセラミックスマトリックス(母材)と複合化した材料です。耐熱合金より軽量(比重は約1/3)で高耐熱、そして壊れにくい(高強度・高靭性)といった特長から、航空機や発電をはじめ、宇宙、自動車など、さまざまな分野に適用が期待されています。
セラミックスの最大弱点を克服した材料
一般的なセラミックスは釘を打つと簡単に割れてしまいますが、CMCは釘を打っても割れません。傷に対する許容性(損傷許容性)を有し、セラミックスの最大の弱点である脆さを克服した材料といえます。
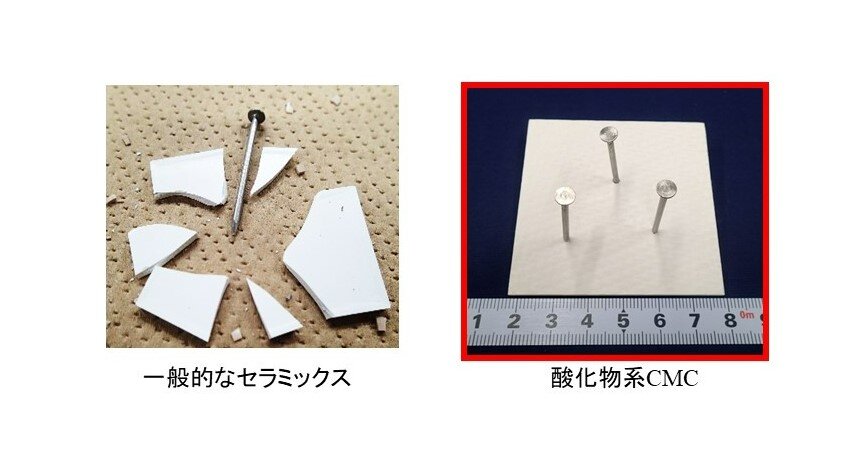
種類
CMCは、非酸化物系と酸化物系の2種類に大きく分けられます。
耐環境性(酸化・水蒸気) | コスト | 耐熱性 | |
---|---|---|---|
非酸化物系CMC | × | × | 〇 |
酸化物系CMC | 〇 | 〇 | × |
酸化物系CMCは、非酸化物系CMCと比べて、酸化や水蒸気雰囲気(水蒸気で満たされた空間)に強く、耐環境性に優れています。また材料コストが安く、比較的簡便な製造工程で済むため、一般的な工業製品への適用が可能です。しかし、耐熱性に関しては1,000℃程度と低く、実用化の大きな壁となっていました。
独自ドーピング技術を開発
酸化物系CMCの耐熱性は、セラミックス繊維の性能で決まります。そこで東ソーは酸化物系CMCの耐熱性が低い原因を調査し、セラミックス繊維を構成する結晶粒が高温中で成長し粗大化することが原因だと突き止めました。そして結晶粒の成長を抑制する方法を模索し、セラミックス繊維中に結晶粒成長を抑制する元素を均質にドーピング*する技術(UDM)の開発に成功しました。
-
結晶の物性を変化させるために少量の不純物を添加すること。ドープとも言う。
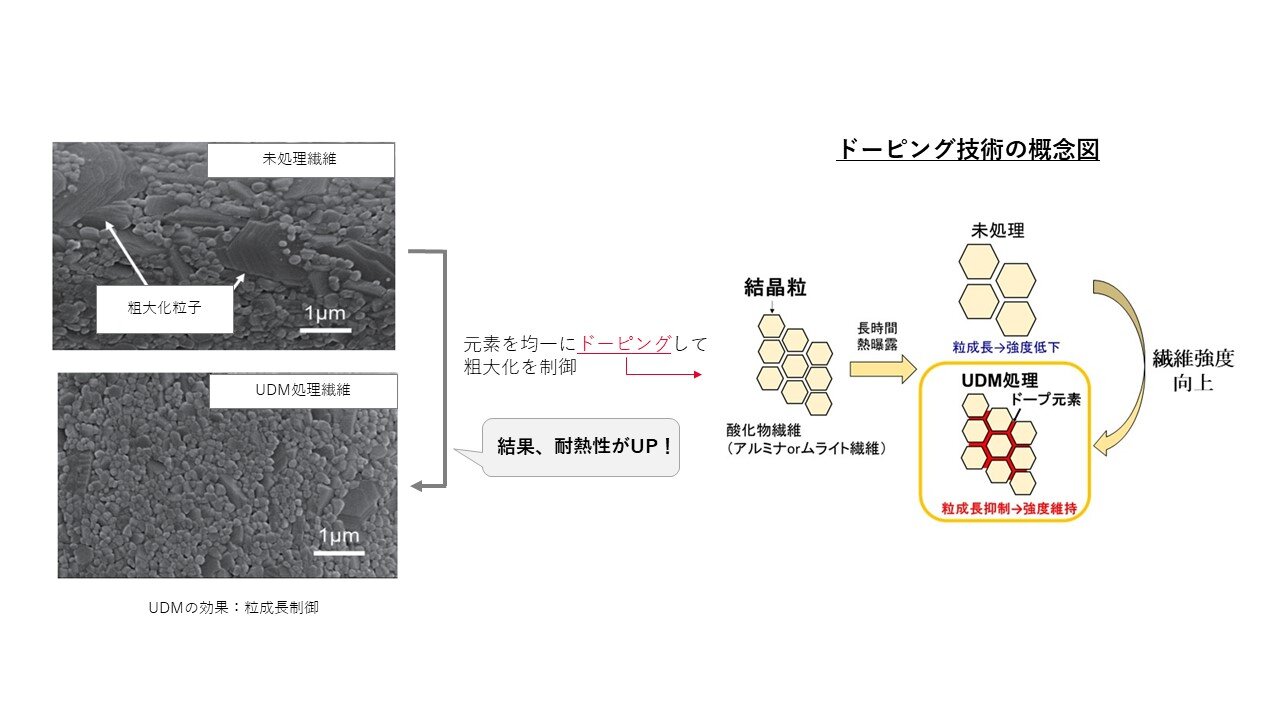
これは東ソー独自の技術です。12μm程度の細い繊維を傷つけず、かつ均質に元素をドーピングする技術の難易度は高く困難でしたが、この技術を用いて作製した酸化物系CMCは、1,200℃中で1,000時間熱にさらしても強度は低下せず、従来の耐熱金属や酸化物系CMCに比べ、耐熱性を大幅に高めることができました。
また開発した酸化物系CMCは形状の自由度が高く、大型化や複雑形状化も可能です。今後はさらに耐熱性を上げることが課題であり、原料や加工技術の工夫を行っていきます。
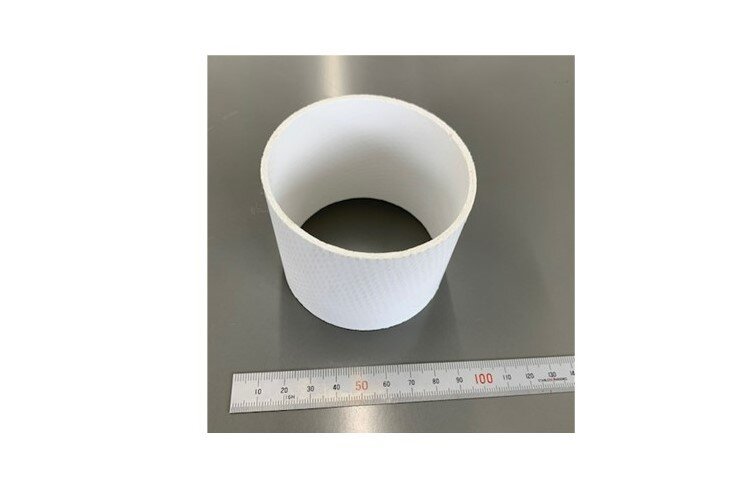
燃費向上・CO2排出削減に貢献
軽量・高耐熱性を併せ持つ当開発品がタービン部材として使用されれば、従来達成できなかったエンジンの高燃費化・CO2排出削減の一助になると考えています。また、耐熱合金の代替として一般的な工業用部材などにも使用可能で、従来では難しかったプロセスの高温化が実現され、省エネにも貢献できると期待しています。
関連情報
研究・技術報告書
おすすめ記事